环氧树脂材料因含有交联结构以及苯环、胺基、羟基和醚键等不饱和键或极性基团,在贮存、使用过程中,易出现各种老化失效现象。具体表现在表面黄化,失去光泽,出现裂纹,整体力学性能下降等,从而影响其使用寿命。总的来说,引起环氧树脂老化的因素分为内因和外因两个方面。
内因主要是材料的成份以及链结构,材料含杂质,比如催化剂残留、添加剂、金属离子、双键和含羰基化合物等。外因是材料所处环境条件,目前环氧树脂常见的老化形式主要有物理老化、热氧老化、湿热老化、光氧老化等,同时还有一些其他的老化形式,比如化学介质老化、电热老化、高能辐射老化,这些条件会诱使材料发生老化降解。环氧树脂老化是一个复杂的过程,通常是内因与外因的共同作用下,环氧树脂分子链发生交联支化或者断链,导致环氧树脂性能劣化。
目前环氧树脂的抗老化措施主要有两类,一类是对环氧本体结构进行改性,减
少容易引起老化的薄弱点;另一类是加入高效的抗老化助剂(如抗黄变剂、光稳定剂、抗氧剂等),减缓光、热、氧、水分等环境因素对环氧树脂的老化降解作用。
热氧老化
环氧制品在含氧环境中受到热,分子链会不断吸收环境中的氧,生成氢过氧化物。氢过氧化物不稳定,会导致聚合物主链发生重排反应,出现断链或交联,使得聚合物材料的性能劣化,出现热氧老化现象。环氧树脂在加工、贮存和使用过程中,基本都会接触到空气,在一定的温度作用下,环氧树脂很容易发生热氧老化。环氧树脂在热氧老化的初期普遍存在后固化现象。当后固化完全后,在热与氧的作用下,环氧树脂主要发生 α 碳上的弱键断裂,生成大量自由基,发生自由基链式反应,分子链结构遭到破坏,生成羰基产物。这个现象大多发生在环氧制品表面,如环氧美缝剂,时间久了容易发生黯淡褪色、发黄、龟裂等现象,这很可能与氧的扩散深度有关。
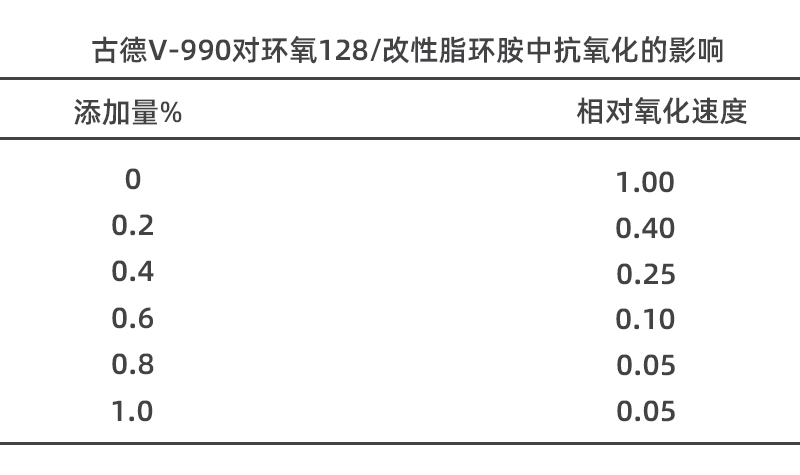
光氧老化
环氧制品的光氧老化机理与热氧老化机理相似,两者的主要区别是光氧老化的引发源较热氧老化多,比如催化剂残留、添加剂、金属离子、双键和含羰基化合物等。环氧树脂在光紫外线作用下为激发态,再分解成自由基与氧反应,生成氢过氧化物,最后引发一系列分子链断裂或交联。环氧树脂含有的苯环和醚键等不饱和键或极性基团,以及聚合阶段和加工过程中带入的杂质容易吸收紫外线产生引发作用,导致环氧树脂发生光氧化反应。
在环氧树脂的光氧老化过程中,羰基发色团的数量不断增加,树脂表面出现黄化。随着老化程度的加深,树脂的表面出现各种黄化、龟裂等现象,导致力学性能出现明显下降。
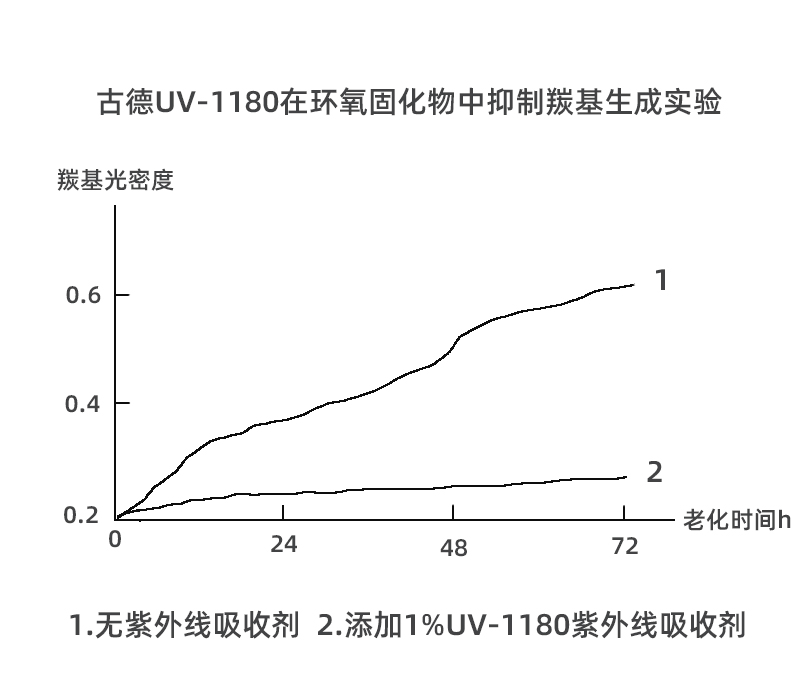
研究表明,当添加紫外线吸收剂UV-1180,紫外光照射导致了环氧树脂羰基密度明显减少,黄化现象也出现明显的下降。这是因为UV-1180将紫外线具破坏力的波段转化为热能从而避免环氧树脂链段化学键破坏、酯羰基结构消失,羟基、芳香族醚和脂肪族醚的下降。
环氧树脂制品常见防老化方法
①通过添加环氧树脂专用的抗氧剂改善热稳定性,添加抗黄变剂、紫外线吸收剂等助剂增强抗日晒性能提高耐候性。如古德UV-1180,V-900,V-990等抗老化助剂,这是目前最常用以及最有效的方法。
②采用比较好的固化剂,促进剂,活性稀释剂及环氧树脂,尽量不采用酚类、叔胺类等易黄变品种的促进剂。
③对环氧树脂进行共聚改性。对环氧树脂结构进行改性,引入硅烷,异氰酸酯等材料的官能团,共聚改性是利用其他单体或聚合物的优点,减少环氧树脂的老化薄弱点,从而增强环氧树脂的抗老化性能。
④加入无机纳米填料。无机纳米填料因其良好的抗热氧、湿热、光氧老化性能以及结构稳定性,在环氧树脂防老化领域受到了极大的关注。